Injection molding uses high pressure to compress molten plastic into the shape of a part. This allows intricate geometries and details that would be impractical for other processes. Read on Injection Molding Tooling Florida for more information.
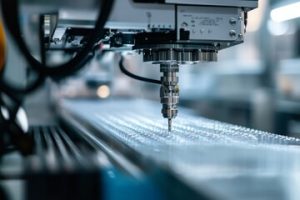
Injection molds can be finished in a variety of ways, including cosmetic textures like leather look, soft touch or sparkle. The type of finish chosen will affect the final cost.
Injection molding is a well-established and cost-effective way to manufacture both short and high-volume runs of complex plastic parts. It involves injecting molten plastic resin into an injection mold under high pressure, then allowing it to cool and solidify. The result is a high-precision finished part that can be ejected from the mold.
The material used in injection molding tooling is crucial, as it affects the quality and durability of the molded part. It also impacts the tooling’s ability to withstand high temperatures and pressures. Injection molding tooling can be made from soft or hard materials. Soft tools are typically best for prototyping and low-volume production runs, while hard tools are ideal for high-volume production runs and longer lifespans.
Injection molds are designed with multiple systems that serve critical functions during the distribution, cooling, and ejection processes. These include sprue bushing, core pins, and gates. These components are designed to meet specific criteria, including dimensional accuracy and compatibility with the molding material. They also play a key role in ensuring consistent and efficient molding cycles.
A sprue bush is the primary passage for the injection of molten plastic into the cavity of the injection mold. The design and quality of the sprue bush directly impact the flow and pressure of the injected plastic, affecting the quality of the molded product. Typical sprue bush designs include standard ones for general applications and custom-designed ones for particular injection pressures or material properties.
Core pins are slender rod-like components used to create internal holes, channels, or cavities in molded parts. Their design and quality directly affect the internal geometry of a part, for both aesthetic and functional reasons. They can be fabricated from standard or custom-designed pins, with varying diameters and shapes.
Gates are the points at which the runner and the core & cavity meet. They’re vital for ensuring proper injection of the plastic, and their placement determines how much of each component will be formed in each mold cycle. Typical gates are designed to be narrower than the runner, so they’re easier to remove from the runner after injection.
Design
Designing injection molding tooling is a complex process that involves many variables. This includes determining the optimal mold size, number of cavities and material choice. It also includes determining the best way to create a uniform surface finish. Adding additional details like undercuts or threads can significantly increase the cost of the mold.
A critical part of injection molds is the sprue bush, which guides the molten plastic into the mold. A well-designed sprue bush can improve ejection speed and reduce waste. Injection molds also require venting to prevent air pockets and shrinkage. These vents can take the form of inserts, ejector pins or drilled holes in the mold. They are essential for achieving consistent quality.
While a high-quality injection mold may seem expensive at first, it will save money in the long run due to reduced maintenance costs and improved part performance. Proper tool care and lubrication can extend the lifespan of the mold. In addition, proper production conditions can minimize wear and tear on the mold.
Another factor that influences the cost of injection molding is the type of material used. Different materials require different temperatures, injection pressures and cooling rates. Some even require different mold designs. For example, a thick section of a part requires more force to eject, which increases cycle times and energy consumption.
Injection molded parts are a mixture of solid and hollow parts. The hollow parts are formed by removing material from the outer surface of the part, while the solid parts are created by injected molten plastic. Injection molding is the ideal solution for combining these parts to create functional products.
A key component of an injection molded part is its dimensional accuracy. Inaccurate dimensions can lead to production problems, such as short shots and warping. Short shots occur when the part isn’t filled completely, which can be addressed by increasing the injection pressure or adjusting the temperature. Warping occurs when the molded part shrinks unevenly. To reduce this issue, designers can add ribs and coring to the B-side of the part to pull the plastic into that area.
Cost
The cost of injection molding depends on a variety of factors. These include the design and material used, production volume, and the type of equipment used. The most significant factor is the tooling cost. This costs thousands of dollars, and it is the first step in manufacturing a plastic injection mold. It is typically fabricated from aluminum or steel, and it includes the negative of the final plastic part. It may also have features like internal water cooling channels and runner systems. It may be treated to achieve specific surface finishes.
The type of plastic is another important consideration in the injection molding process. Different plastics have different properties, and some are more expensive than others. The injection molding process uses a large amount of pressure to compress the plastic, so choosing the right material is crucial to reducing costs. It is possible to save money by using an alternative polymer, such as Polypropylene (PP), which is less expensive than other engineering-grade materials.
Injection molding is a labor-intensive process, and machining the mold components is expensive. This is why it is important to minimize the number of components in your injection-molded plastic parts and to avoid unnecessary features. Also, try to reduce the size of the plastic part to reduce the weight and cost of the finished product. This will also improve the efficiency of the injection molding process and help you to reduce costs.
Production volume is a key factor in determining the per-part cost of injection molding. High-volume demand requires durable materials like hardened steel, whereas low-volume orders can use cheaper aluminum or pre-hardened steel. Additionally, optimizing cycle times increases the production rate and decreases the overall cost of the injection molded plastic part.
Injection molded plastics can require finishing services, such as sandblasting or powder coating, to increase their aesthetics and function. These secondary processes are separate from the injection molding process, and can add to the total injection molding cost. Another way to save money is by avoiding intricate cosmetic details on parts where aesthetics are not critical. This can simplify the mold design and reduce the number of cavities, which lowers manufacturing costs.
Production
Injection molding tooling plays a critical role in turning molten plastic into finished, dimensionally-accurate parts. It comprises an intricate set of systems, including distribution, cooling, and ejection systems that work together to transform a raw material into a finished product. Choosing the right injection mold for your project depends on factors such as part volume, annual usage, and cost. For example, for high-volume production, multi-cavity tools rated to last millions of cycles can reduce per-part costs and improve productivity.
Mold production begins with detailed mold design, where engineers translate product specifications into a physical 3D model using computer-aided design (CAD) and computer-aided manufacturing (CAM) software. Once the mold is fabricated, it can be used to produce samples and prototypes that can be tested for quality and manufacturability. This allows the product to be refined before committing to full-scale production, resulting in significant savings in time and resources.
Proper mold maintenance is critical to extending the life of injection molding tools. Regular cleaning and lubrication help prevent wear, which can lead to costly repairs down the line. Keeping the mold in optimum condition can also improve performance and quality, ensuring that it runs efficiently and within specification.
The choice of tooling materials also impacts cost and quality. Durable materials like hardened steel are preferable for high-volume production runs, while aluminum and pre-hardened steel are suitable for lower-volume applications. The material’s temperature and pressure tolerances should also be considered, as well as its sensitivity to moisture, which can result in surface defects or internal weaknesses.
During the injection molding process, a distribution system transports the melted plastic from the nozzle to the core and cavity. A cooling system then helps the molded plastic to harden into its final shape. An ejection system is then used to eject the cooled, hardened plastic from the mold. Depending on the type of injection mold, the ejection system can consist of angular slides that move at an angle to the mold opening, lifters that move vertically to create recessed features, or hydraulic or mechanical cylinders.
Injection molds can be prone to a variety of problems, including sink marks, flow lines, and surface delamination. These issues can occur because of a number of reasons, such as excessive injection temperatures or improper mold release. In order to avoid these issues, it is important to use an experienced injection molding manufacturer with a proven track record.